Pentair Machine Vision –
a close-up look.
One of the most exciting innovations in 21st century manufacturing is Artificial Intelligence. Pentair has been quick to embrace this by introducing Machine Vision to its European manufacturing lines.
Pentair has already deployed this cutting-edge technology in the assembly of components and for the collation of replacement parts. It has pushed reliability, consistency and productivity to new heights.
Salvatore Licitra, Pentair Manufacturing Manager, explains how Machine Vision is transforming quality at Pentair.
“We started using Machine Vision at our Pisa manufacturing ‘Centre of Excellence’ in 2020. Initially we wanted to increase reliability and consistency on our replacement parts line. We also wanted to drive up quality by using it to detect any irregularities in our production lines.
Machine Vision Identification
We installed the first workstations in our pick ‘n pack area – where replacement parts are collected together before being shipped to the customer.
We all know that water treatment can be a tough environment and parts do need replacing. That’s disruption enough but no-one wants to find they have been sent the wrong replacement part.
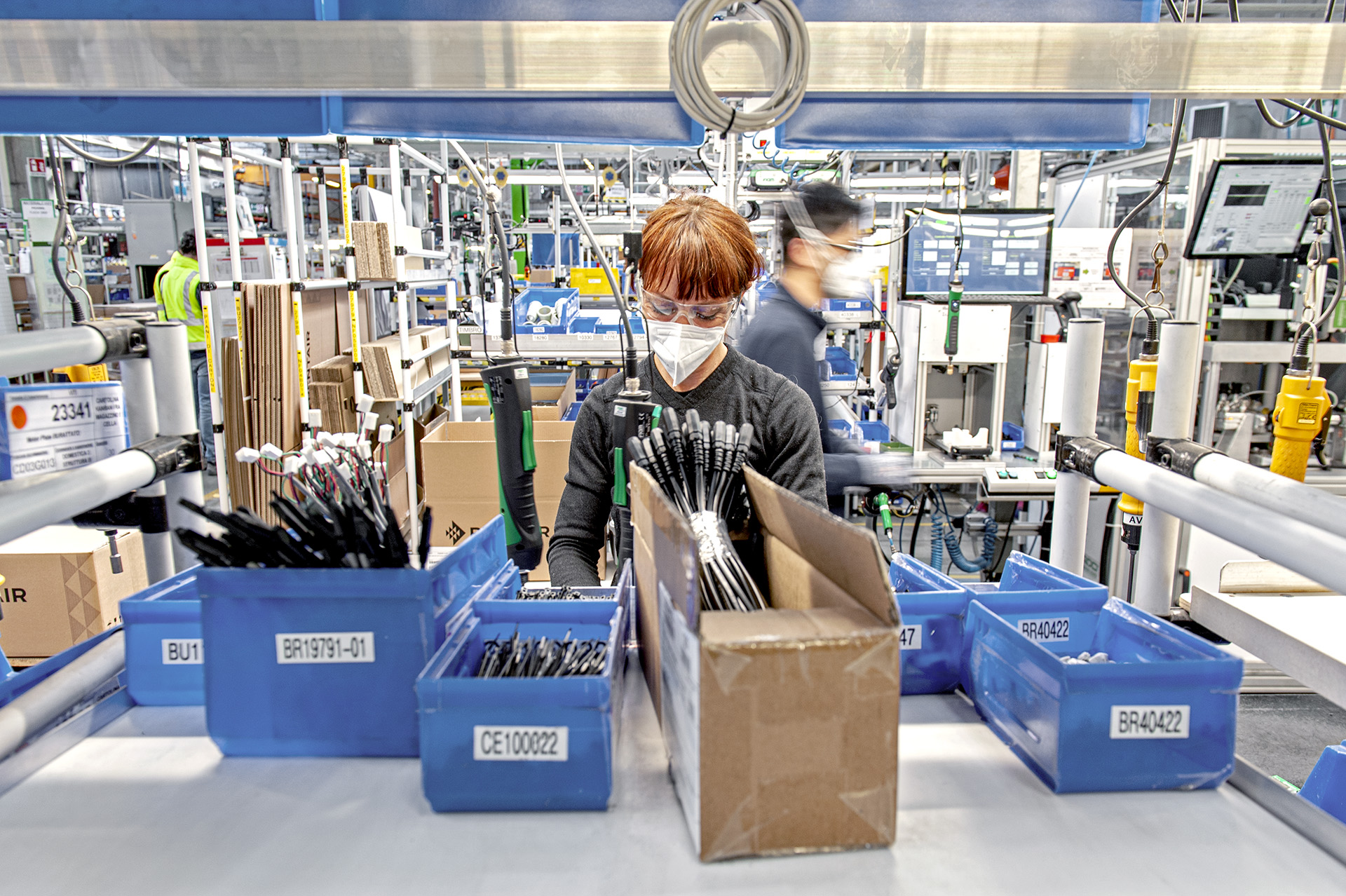
Essentially our Machine Vision workstations comprise a ‘smart’ high-definition camera with sophisticated image processing capability, that can inspect and validate parts and assemblies in milliseconds.
They identify and check bagged contents for part number, size, shape, weight, colour, barcode and many other criteria against the customer’s order. This eliminates any possibility of human error and our customers always receive what they ordered.
Thanks to our investment in Machine Vision for replacement parts, returns are a thing of the past. We hardly ever get parts back from our customers anymore – so it is working!”
Machine Vision Inspection
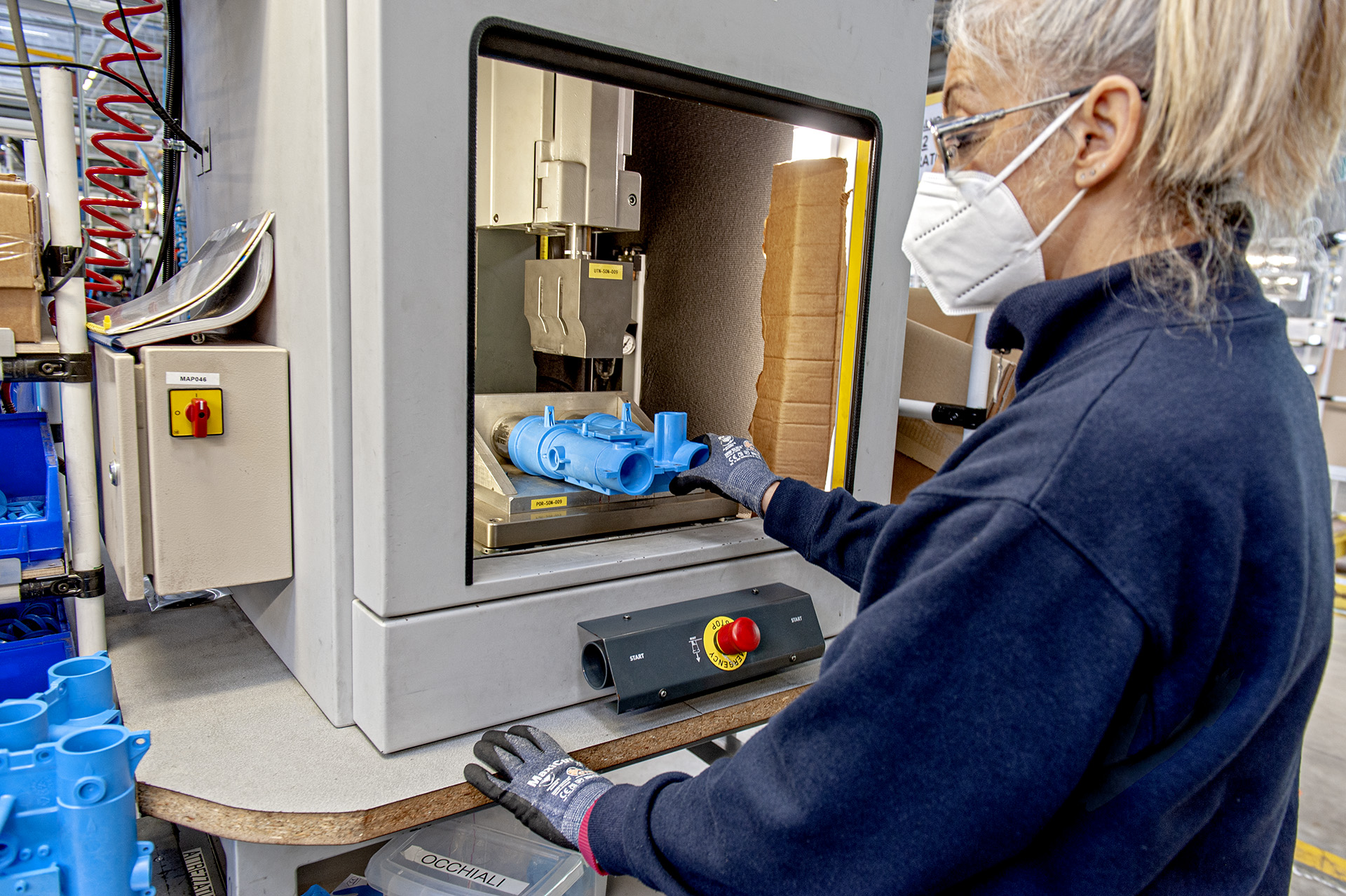
Around the same time, we started using Machine Vision for inspection testing in the production of Pentair valves, especially the pistons and flow washers, which are critical to valves working correctly.
Historically, we have relied on the test bench to perform an end-check on all our valves, but in many ways it is not very precise. For example, if the valve flow rate or pressure readings are not correct, we would need to reject the whole valve or unpick it to find out what was wrong. Machine Vision inspection changes all that.
Our Machine Vision inspection workstations check each part and process, in series, before and during the assembly.
The first workstation checks the shape and profile of the piston, testing and checking for any defects. In a fraction of a second, it either fails or is cleared to go to the next stage. A second workstation verifies the correct dimension of the corresponding flow washer for the piston. Again, it needs to pass multiple criteria, at speed, before moving to the next stage. A third workstation checks the final assembly against pre-loaded parameters before it will pass.
Each Machine Vision check is made ‘on the fly’ in milliseconds, with alarms triggered if there are any issues. Scrappage rates are minimal as the valve is effectively tested before it even gets to the test bench.
Traceability
Traceability is increasingly important to us, and our customers, especially in some sectors like food service where we are required to keep detailed records of manufacturing batches. With Machine Vision, each process and every assembly is documented with data and images. Apart from helping with the continuous improvement of our manufacturing processes, this makes traceability bulletproof.
It is hard to overstate the positive impact Machine Vision has had on quality at Pentair. Our accuracy and precision have improved, we have increased the speed and volume of production with almost zero defects and our reduced reliance on manual inspection means more quality is assured across the board.
Part of our quality commitment is zero-defect so we are planning more investment in Machine Vision technology. We put our trust in that technology as our customers place their trust in us.”