Pentair Supertanks –
made to measure, last a lifetime
Composite pressure vessels are lighter, stronger and more versatile than metal tanks, and they last a lifetime with little or no maintenance. And customers can configure their own bespoke tank design with up to a million permutations. We find out what is so super about Pentair Supertanks.
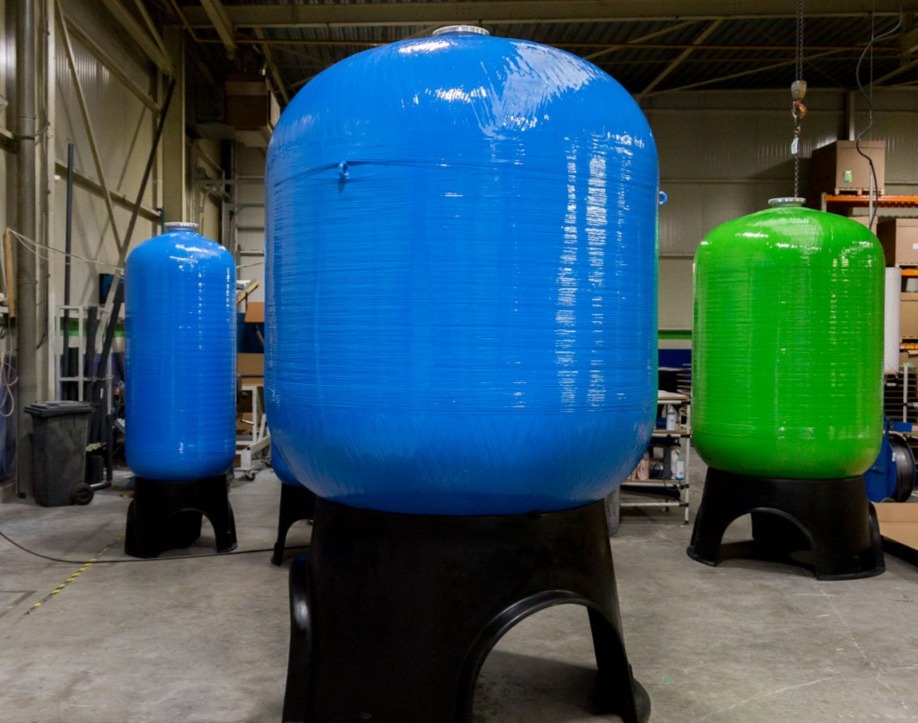
When it comes to long-term liquid storage, composite pressure tanks are a no-brainer. With a corrosion resistant plastic liner and reinforced fibreglass outer, they are lighter, stronger and longer-lasting than metal alternatives. No wonder composite tanks have become the go-to choice for pressurised fluids. And the chances are, your tank started life at our Herentals plant in Belgium, Europe’s leading tank production facility.
However, what if you need something that’s made-to-measure? Something bigger than usual? Tall and thin or short and fat? What if you need a one-off, with non-standard connections, openings or sight holes? Thinking metal? Think again.
Using cutting-edge technology and advance polymer welding skills, Pentair can offer all the benefits of composite tanks at almost any size, volume and pressure requirement.
One size does not fit all
“We are the only company who can offer composite tank customisation on this scale”, says Matteo Rota, Global Category Leader for Pressure Vessels at Pentair. “One size does not fit all and we appreciate that engineers want, and need, to be able to specify certain tanks. But there is an industry mindset that customisation means steel fabrication. However, we can offer our core product, a composite fibreglass pressure tank, with over a million customer-specified permutations! Supertanks have all the advantages of our off-the-shelf catalogue yet are made-to-measure to the exact user specification required.”
A history of innovation
This industry-first is part of a history of innovation from the Pentair family. It was over 60 years ago that the company first revolutionised the water treatment industry by introducing small composite pressure vessels – tanks that would later be specified by NASA for its Apollo space programme.
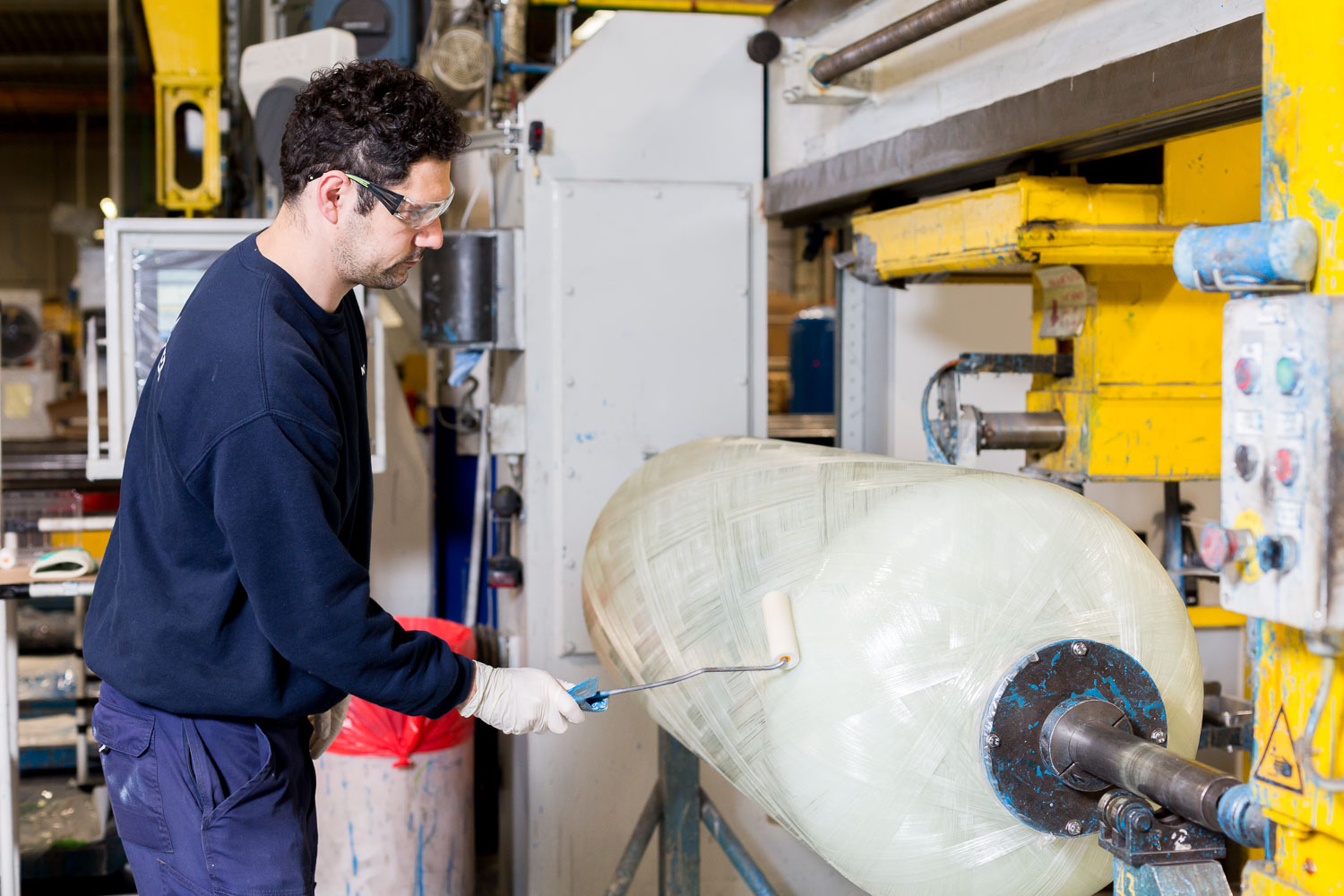
“Today’s composite tanks work on the same principal as those early tanks,” explains Matteo. “A thermoplastic, moulded liner gives the tank its basic shape. The liner can be polyethylene (PE) for standard water treatment or high non-reactive polyvinylidene fluoride (PVDF) for chemicals, solvents or acids. Either way the liner is seamless, clean, non-corrosive and offers 100% contamination protection.”
“The liner is then wrapped in a mix of fibreglass and epoxy resin to give it strength and stability. The result is a super-strong tank that is less than half the weight of a metal equivalent. They are 100% corrosion free, won’t react with their contents and require zero maintenance. And using automated 3D modelling software we are also able to streamline the production of one-off, custom-made composite tanks.”
Advanced 3D modelling software makes customisation easy
“We recognised that there is a demand for non-standard and oversized tanks, especially in the municipal, heavy commercial and industrial applications”, continues Matteo. “Through precision cutting and specialist welding technologies we can accommodate much larger composite tanks, up to 8000 litres capacity.”
“Customisation is quick and simple. Using a specification form, customers choose the required diameter, liner material, volume and colour, along with any mounting or base type. The customer can also specify the distribution system within the tank, connection types, and of course any openings, apertures and accessories required. Once we have that form, we input all these specs into an online configuration tool which generates a rendered technical drawing and a quotation within minutes. We plan to release that online tool direct for customer use within the coming months.”
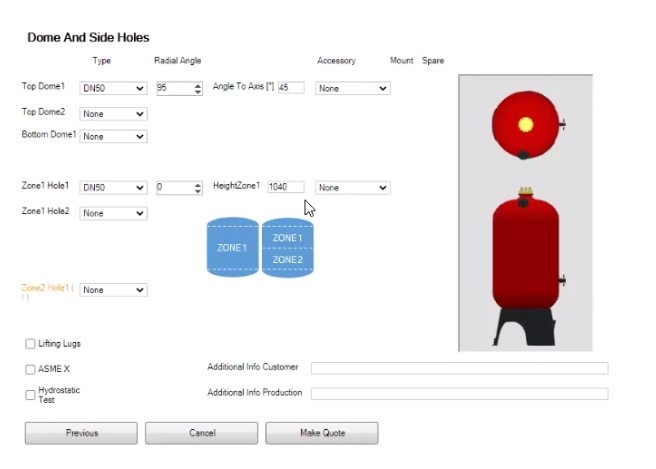
“As you can imagine customers who have historically used steel tanks have been delighted. Not only is it a better solution, but the cost is highly competitive with steel. And when you factor in the reduced transport cost and long-term reduction in maintenance cost it’s a win-win-win. As the price of steel spirals, we have seen increasing orders from food service, electronics, healthcare and municipal sectors – especially where desalination is a requirement.”
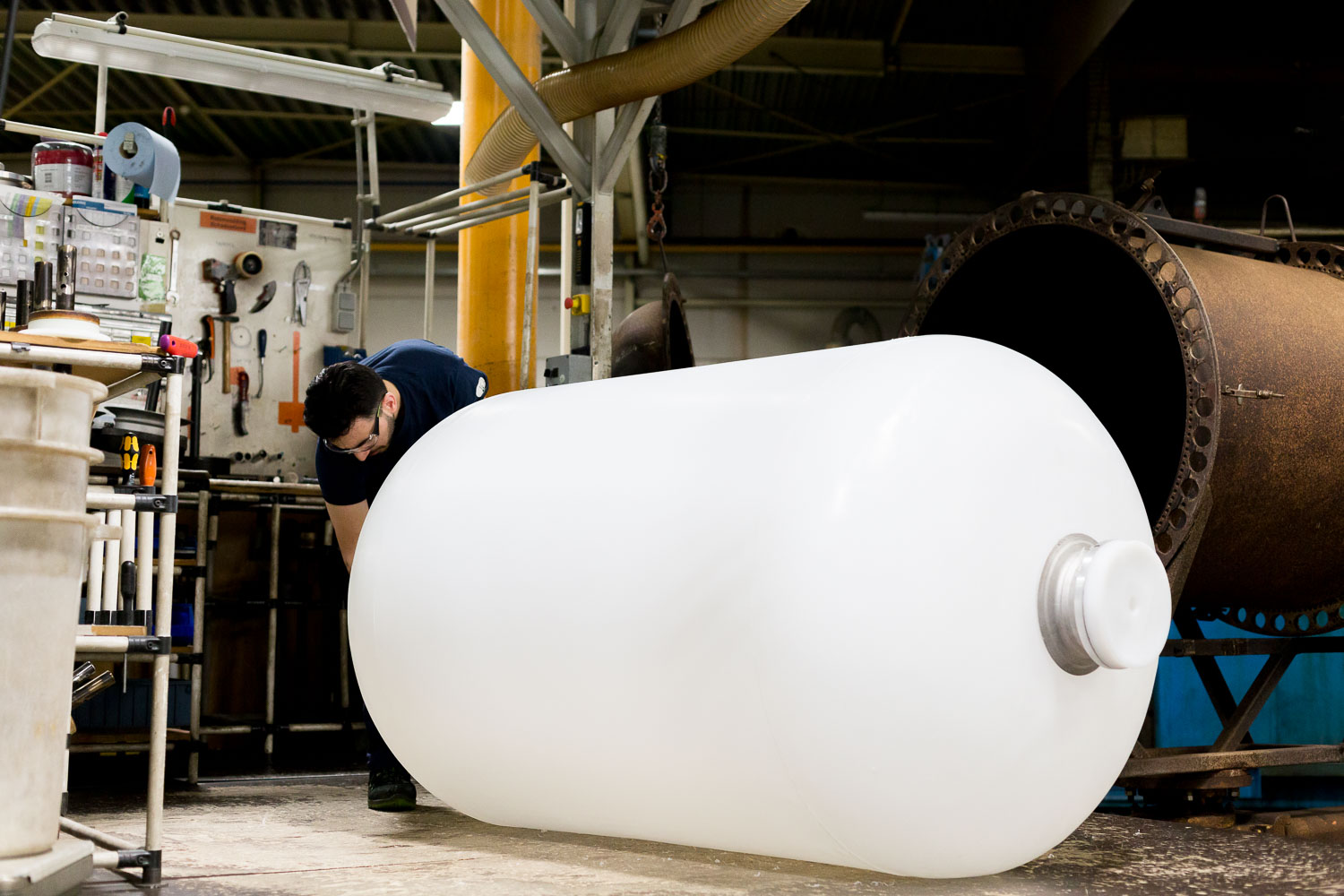
Choosing a composite Supertank will repay you for life
Pentair custom made composite Supertanks are truly unique. They are made at our Herentals plant in Europe but attract orders across the globe. So, next time you have a requirement for a new Supertank or are overhauling an existing large installation that needs a new pressure vessel, think composite. Don’t just pick up the phone to your steel tank supplier, take a look at a Pentair Supertank – it will repay you for years to come.
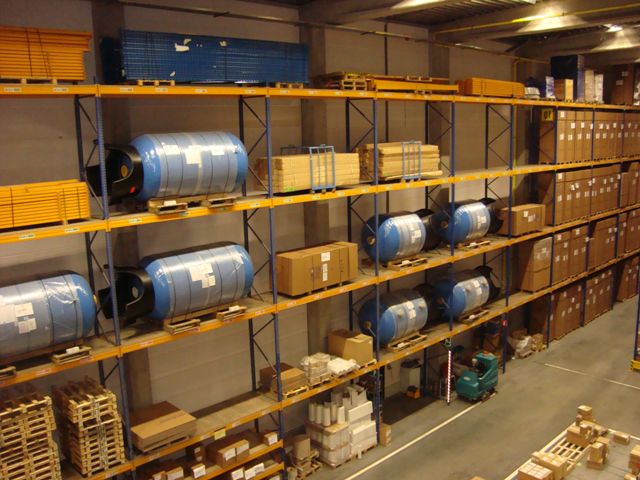