Pentair Operational Taskforce pulls out all the stops
It’s late Friday and many businesses have already closed for the weekend. But a few screens are still alight across Europe and the conversation will run late into the evening. The Pentair Operations Taskforce has swung into action.
It is meeting, as it does every Friday, to make sure there are no hidden surprises on Monday morning. What external issues will impact production? What contingencies can be put in place? What alternative solutions can be proposed? And how can Pentair customers be guaranteed continuity of supply? And it’s not even dark yet.
Why the supply chain has slowed down
Across the globe, every industry is being impacted by a supply chain that is frankly buckling. The reasons are many fold and complex. Expectedly many are COVID related. With raw material production disrupted, consumer demand now high and economies struggling to bounce back, there is a shortage of everything from plastics to metals. The pandemic has also had a knock-on impact on transport with a world-wide bottleneck in shipping and road transport that just can’t catch up. Add to this a worldwide ‘semiconductor famine’ and you have a perfect storm that makes predictability of supply a potential lottery. After decades of ‘just-in-time’ manufacturing, just-in-time just got late.
If you fail to plan, you are planning to fail
Everyone is impacted and Pentair is no exception. Decisive action is required, and Pentair has a well-established process in place to get the job done. Its Operations Taskforce is a highly experienced team with a history of risk-based thinking, established five years ago for exactly this scenario – to monitor factors that impact production and rapidly act to mitigate any disruption.
In better times it meets fortnightly, though the current situation has put it on amber alert and during 2021, meetings have been a minimum of every week.
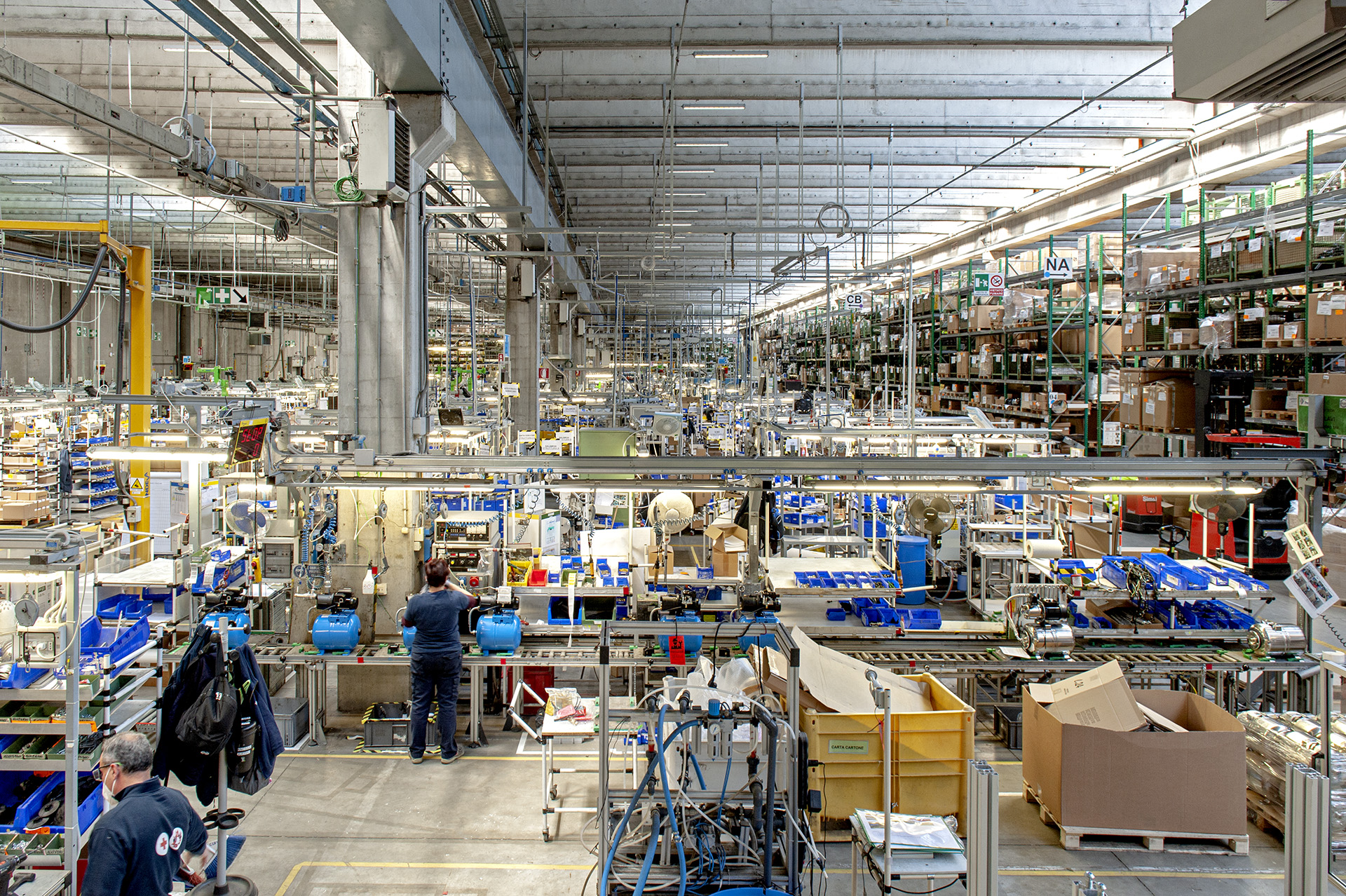
We are thinking outside the box
“The work of the Operations Taskforce is part of our risk-based thinking,” explains Marco Calatroni. There is no-one better placed than Marco to bring insight to the task force. As Head of Value Stream at Pentair, he has his finger on the pulse of Pentair European production with a remit that extends from new product development to production scheduling. His role is to improve efficiency and reduce waste and now his skills are being tested by a shortage of raw materials and components that is leaving stockrooms empty.
“It’s a juggling act but we see it as an opportunity to learn too”, he continues. “To minimise the delay to our customers we have to be as creative as possible. We have discovered opportunities to substitute similar or better components, with no impact on performance. It might take a little adaptation, but that can be a good thing in the long run.”
Turning words into action
Just this month Pentair has reworked, modified and adapted components on two major product lines: the Autotrol 255 valve and the SIATA V132 valve.
“For the Autotrol, we temporarily hand-machined a new top distributor, a shortage of which was impacting our ability to supply.” continues Marco. “We reworked a similar Fleck distributor to make it a perfect fit and will ship with these until a new mould can be developed by our European component supplier. For some of the same range, we have also developed a new aircheck adaptor kit to bridge a gap in supply of the aircheck bowl. Meanwhile transformers for the SIATA V132 valves are temporarily unavailable to us, so we are shipping with an adapted Autotrol transformer, again to maintain supply.”
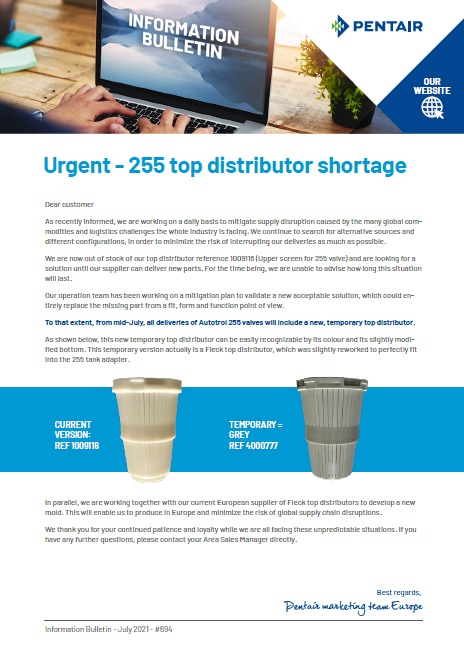
“In each case, it involves planning, testing, sometimes machine working, all with considerable documentation even for the smallest change. But it is worth it to keep our customers and their businesses running. We also try to allocate supply to prevent anyone stockpiling. It’s tough but the fairest way to share shortages across all our customers, large and small. We have to be agile and make quick decisions, but I am confident we will emerge stronger as a result.”
Seeing the complete picture
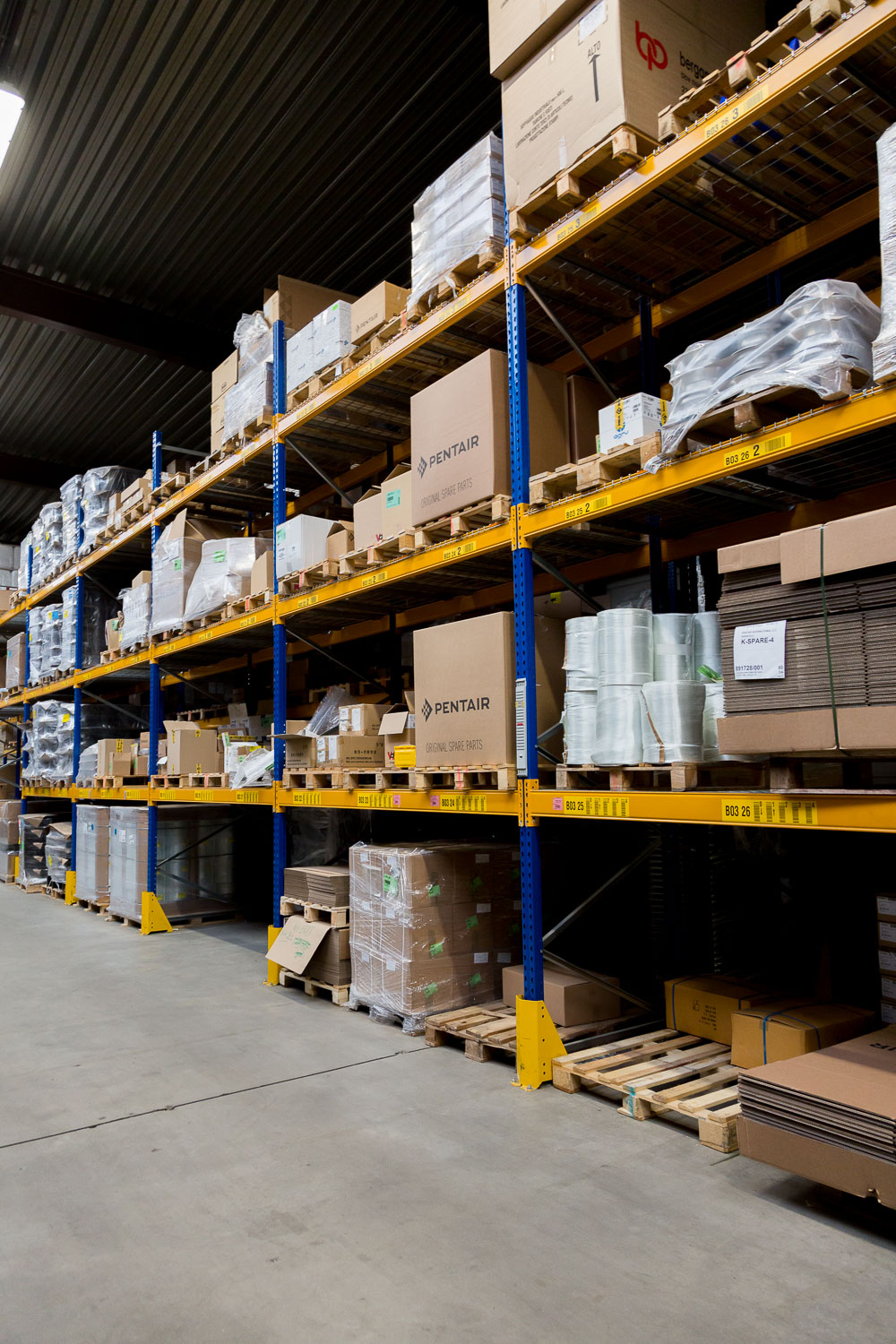
Marco is joined each week by key stakeholders from production, procurement, and product management who make up the Operations Taskforce. Armed with a detailed knowledge of what has been planned for production and any potential supply shortages, they systematically work through every product line, identify what (if any) are impacted and what can be done to lessen any disruption.
“Our objective is to build a comprehensive ‘problem’ dashboard – the good, the bad and the ugly,” says Eliane Poey LaFrance, Product Manager for Valves. “It’s how we get a complete and accurate picture. Only then can we take action and we give an honest appraisal to our customers."
“It can be a tough meeting. We all have a role to play and we hold each other to account – there are some tough questions and difficult decisions. But we are an empowered team. We have the autonomy and flexibility to be able to make major production changes at speed. That could be changing a supplier, prioritising a production run or adapting a component. Whatever it takes. Just this month we have been hand-machining components to replace parts that are on a long back order. The customer will actually get a superior product as a result and delivered ahead of expectation.”
Getting through it together
The Operational Taskforce is the best way to manage a difficult situation”, agrees Marco Calatroni. “Our dashboard tells the whole story so we can best mitigate issues and be open with ourselves and our customers.”
“And in return our customers have been loyal as they understand what we are trying to achieve. No-one likes to receive something later than hoped, but hidden surprises are even worse. If you know in advance, you can plan for it.”
“We are all in the same boat”, concludes Marco. “Our materials suppliers, our distributors, our customers and competitors are all struggling with the same issues. But we are steering towards calmer water with the best crew at the helm. The Pentair way is forward-thinking, being proactive and we are committed to finding solutions that will get us all through this together.”